Intro
Streamline construction projects with a Material Take Off Sheet Excel Template, featuring automated quantity calculations, cost estimation, and bill of materials management for efficient building planning and budgeting.
The construction industry relies heavily on accurate material takeoff to ensure projects are completed on time and within budget. A material takeoff sheet is a document that lists all the materials needed for a construction project, along with their quantities and costs. Creating a material takeoff sheet can be a tedious and time-consuming process, but using an Excel template can simplify the task.
In recent years, the use of technology has become increasingly prevalent in the construction industry. One of the key benefits of using technology is the ability to streamline processes and improve efficiency. A material takeoff sheet Excel template is a valuable tool that can help contractors, architects, and engineers to quickly and accurately estimate the materials needed for a project.
The importance of accurate material takeoff cannot be overstated. A mistake in the material takeoff can lead to delays, cost overruns, and even project failure. Therefore, it is essential to use a reliable and efficient method for creating a material takeoff sheet. An Excel template is an ideal solution, as it allows users to easily customize and update the template to suit their specific needs.
Using a material takeoff sheet Excel template offers numerous benefits, including increased accuracy, improved efficiency, and enhanced collaboration. The template can be shared with team members, stakeholders, and suppliers, ensuring that everyone is on the same page. Additionally, the template can be easily updated and revised as the project progresses, reducing the risk of errors and discrepancies.
What is a Material Take Off Sheet?

A material takeoff sheet is a document that lists all the materials needed for a construction project, along with their quantities and costs. The sheet is typically created during the pre-construction phase and is used to estimate the total cost of the project. The material takeoff sheet is an essential tool for contractors, architects, and engineers, as it helps them to plan and manage the project effectively.
The material takeoff sheet typically includes the following information:
- Material description
- Quantity
- Unit cost
- Total cost
- Supplier information
Benefits of Using a Material Take Off Sheet Excel Template

Using a material takeoff sheet Excel template offers numerous benefits, including:
- Increased accuracy: The template helps to reduce errors and discrepancies, ensuring that the material takeoff is accurate and reliable.
- Improved efficiency: The template saves time and effort, allowing users to quickly and easily create a material takeoff sheet.
- Enhanced collaboration: The template can be shared with team members, stakeholders, and suppliers, ensuring that everyone is on the same page.
- Customization: The template can be easily customized to suit specific needs and requirements.
- Cost savings: The template helps to reduce costs by minimizing waste and ensuring that the right materials are ordered in the right quantities.
How to Create a Material Take Off Sheet Excel Template
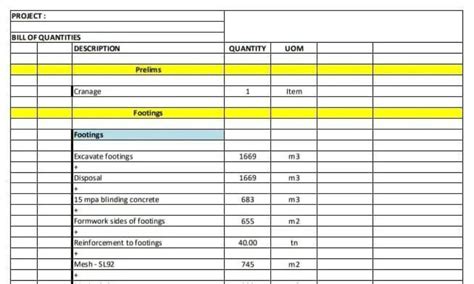
Creating a material takeoff sheet Excel template is a straightforward process that involves the following steps:
- Determine the scope of the project: Identify the materials needed for the project and the quantities required.
- Set up the template: Create a new Excel spreadsheet and set up the template with the following columns: material description, quantity, unit cost, total cost, and supplier information.
- Enter the data: Enter the material data into the template, including the description, quantity, unit cost, and total cost.
- Calculate the totals: Use formulas to calculate the total cost of each material and the total cost of the project.
- Customize the template: Customize the template to suit specific needs and requirements, such as adding additional columns or rows.
Tips for Using a Material Take Off Sheet Excel Template

Here are some tips for using a material takeoff sheet Excel template:
- Use clear and concise language: Ensure that the material descriptions and quantities are clear and concise, avoiding any ambiguity or confusion.
- Use formulas: Use formulas to calculate the totals, ensuring that the calculations are accurate and reliable.
- Use conditional formatting: Use conditional formatting to highlight any errors or discrepancies, making it easier to identify and correct mistakes.
- Regularly update the template: Regularly update the template to reflect any changes to the project, ensuring that the material takeoff is accurate and up-to-date.
Common Mistakes to Avoid When Using a Material Take Off Sheet Excel Template

Here are some common mistakes to avoid when using a material takeoff sheet Excel template:
- Inaccurate data: Ensure that the material data is accurate and reliable, avoiding any errors or discrepancies.
- Insufficient customization: Ensure that the template is customized to suit specific needs and requirements, avoiding any ambiguity or confusion.
- Failure to update the template: Regularly update the template to reflect any changes to the project, ensuring that the material takeoff is accurate and up-to-date.
- Inadequate collaboration: Ensure that the template is shared with team members, stakeholders, and suppliers, ensuring that everyone is on the same page.
Best Practices for Managing a Material Take Off Sheet Excel Template

Here are some best practices for managing a material takeoff sheet Excel template:
- Regularly review and update the template: Regularly review and update the template to reflect any changes to the project, ensuring that the material takeoff is accurate and up-to-date.
- Use version control: Use version control to track changes to the template, ensuring that all stakeholders are aware of any updates or revisions.
- Collaborate with team members: Collaborate with team members, stakeholders, and suppliers to ensure that everyone is on the same page.
- Use clear and concise language: Ensure that the material descriptions and quantities are clear and concise, avoiding any ambiguity or confusion.
Material Take Off Sheet Image Gallery

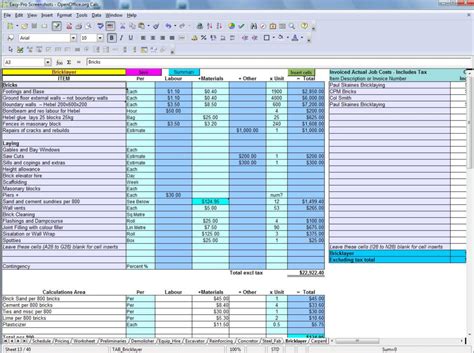






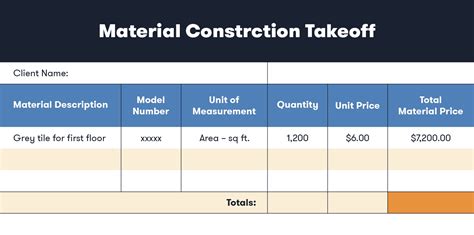

What is a material takeoff sheet?
+A material takeoff sheet is a document that lists all the materials needed for a construction project, along with their quantities and costs.
Why is a material takeoff sheet important?
+A material takeoff sheet is important because it helps to ensure that the right materials are ordered in the right quantities, reducing the risk of delays and cost overruns.
How do I create a material takeoff sheet Excel template?
+To create a material takeoff sheet Excel template, determine the scope of the project, set up the template, enter the data, calculate the totals, and customize the template to suit specific needs and requirements.
What are the benefits of using a material takeoff sheet Excel template?
+The benefits of using a material takeoff sheet Excel template include increased accuracy, improved efficiency, enhanced collaboration, and cost savings.
How do I manage a material takeoff sheet Excel template?
+To manage a material takeoff sheet Excel template, regularly review and update the template, use version control, collaborate with team members, and use clear and concise language.
In conclusion, a material takeoff sheet Excel template is a valuable tool for contractors, architects, and engineers. By using a template, users can quickly and easily create a material takeoff sheet, reducing the risk of errors and discrepancies. The template can be customized to suit specific needs and requirements, and it can be shared with team members, stakeholders, and suppliers to ensure that everyone is on the same page. By following the tips and best practices outlined in this article, users can get the most out of their material takeoff sheet Excel template and ensure that their construction projects are completed on time and within budget. We encourage you to share your thoughts and experiences with material takeoff sheets in the comments below, and to share this article with anyone who may benefit from it.