Intro
Boost construction efficiency with 5 lumber takeoff tips, including material estimation, digital tools, and quantity calculation, to streamline building projects and reduce errors in lumber measurement and construction costing.
The construction industry relies heavily on accurate estimates and takeoffs to ensure projects are completed on time and within budget. One crucial aspect of this process is the lumber takeoff, which involves calculating the exact amount of lumber required for a project. Inaccurate lumber takeoffs can lead to delays, cost overruns, and even project failures. To help you improve your lumber takeoff skills, we've compiled five essential tips to consider.
Lumber takeoffs are a critical component of the construction planning process, as they enable contractors and builders to estimate the materials needed for a project accurately. A well-executed lumber takeoff can help prevent errors, reduce waste, and save time and money. With the increasing complexity of construction projects, it's essential to have a solid understanding of lumber takeoff principles and best practices. Whether you're a seasoned contractor or just starting out, these tips will help you refine your skills and improve your chances of success.
The importance of accurate lumber takeoffs cannot be overstated. A single mistake can have far-reaching consequences, from delayed project timelines to significant cost overruns. Moreover, inaccurate takeoffs can lead to material waste, which not only increases costs but also harms the environment. By following these five lumber takeoff tips, you'll be able to minimize errors, optimize material usage, and ensure your projects are completed efficiently and effectively.
Lumber Takeoff Fundamentals

Understanding Lumber Types and Sizes
Lumber comes in various types, including dimensional lumber, engineered wood products, and specialty lumber. Each type has its unique characteristics, advantages, and applications. For instance, dimensional lumber is commonly used for framing, while engineered wood products are often used for roofing and flooring. Understanding the different lumber types and their uses will help you make informed decisions during the takeoff process.Tip 1: Use Accurate Plans and Specifications

Verifying Plan Accuracy
Verifying plan accuracy involves checking for any errors, omissions, or discrepancies in the plans and specifications. This includes reviewing the plans for any changes or updates, as well as checking for consistency in the notation and terminology used. By verifying plan accuracy, you can ensure that your lumber takeoff is based on reliable and trustworthy information.Tip 2: Break Down the Project into Components

Identifying Project Components
Identifying project components involves reviewing the plans and specifications to determine the various elements that make up the project. This includes identifying the different types of lumber required for each component, such as framing lumber, roofing lumber, and flooring lumber. By identifying the project components, you can create a detailed and accurate lumber takeoff that reflects the specific needs of the project.Tip 3: Use Lumber Takeoff Software

Benefits of Lumber Takeoff Software
The benefits of lumber takeoff software include increased accuracy, reduced errors, and improved efficiency. These software programs can also help you manage and track changes to the project, ensuring that your estimates remain up-to-date and accurate. By using lumber takeoff software, you can save time and money, while also improving the overall quality and accuracy of your lumber takeoffs.Tip 4: Consider Waste and Scrap Factors

Calculating Waste and Scrap Factors
Calculating waste and scrap factors involves estimating the amount of lumber that will be wasted or scrapped during the construction process. This can include factors such as cutting waste, handling damage, and excess material. By calculating waste and scrap factors, you can ensure that your estimates are comprehensive and accurate, reducing the risk of errors and inaccuracies.Tip 5: Review and Verify Your Takeoff

Verifying Takeoff Accuracy
Verifying takeoff accuracy involves reviewing your estimates and calculations to ensure that they are accurate and comprehensive. This includes checking for errors, omissions, and discrepancies, as well as verifying your takeoff with the project plans and specifications. By verifying takeoff accuracy, you can ensure that your estimates are reliable and trustworthy, reducing the risk of errors and inaccuracies.Lumber Takeoff Image Gallery


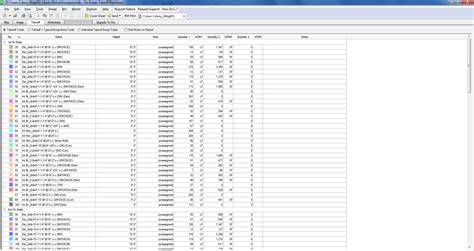







What is a lumber takeoff?
+A lumber takeoff is an estimate of the amount of lumber required for a construction project.
Why is it important to use accurate plans and specifications?
+Using accurate plans and specifications ensures that your lumber takeoff is based on reliable and trustworthy information, reducing the risk of errors and inaccuracies.
How can I improve my lumber takeoff skills?
+You can improve your lumber takeoff skills by practicing, using lumber takeoff software, and staying up-to-date with the latest industry developments and best practices.
What are the benefits of using lumber takeoff software?
+The benefits of using lumber takeoff software include increased accuracy, reduced errors, and improved efficiency.
How can I ensure that my lumber takeoff is accurate and comprehensive?
+You can ensure that your lumber takeoff is accurate and comprehensive by reviewing and verifying your takeoff, using accurate plans and specifications, and considering waste and scrap factors.
By following these five lumber takeoff tips, you can improve the accuracy and completeness of your estimates, reduce the risk of errors and inaccuracies, and ensure that your construction projects are completed efficiently and effectively. Remember to use accurate plans and specifications, break down the project into components, use lumber takeoff software, consider waste and scrap factors, and review and verify your takeoff. With practice and experience, you can become proficient in lumber takeoffs and take your construction business to the next level. We encourage you to share your thoughts and experiences with lumber takeoffs in the comments section below, and don't forget to share this article with your colleagues and friends who may benefit from these tips.