Intro
Discover expert 5 Laser Cut Coaster Tips for precise cutting, using laser engraver machines, and optimizing wood coaster designs with intricate details and custom patterns.
The art of laser cutting has revolutionized the way we create and design various products, including coasters. With the ability to precision-cut intricate designs and patterns, laser cut coasters have become a popular choice for those looking to add a touch of elegance and sophistication to their homes. However, creating the perfect laser cut coaster requires some know-how and expertise. In this article, we will delve into the world of laser cut coasters and provide you with 5 valuable tips to help you create stunning and functional coasters.
Laser cut coasters offer a unique combination of form and function, making them an excellent addition to any room. Not only do they protect your furniture from water marks and spills, but they also add a decorative touch that can enhance the overall aesthetic of your space. Whether you're a DIY enthusiast or a professional designer, laser cut coasters are a great way to showcase your creativity and attention to detail. With the right techniques and materials, you can create coasters that are both beautiful and durable.
The process of creating laser cut coasters involves several steps, from designing the pattern to cutting the material. The key to success lies in understanding the capabilities and limitations of laser cutting technology, as well as the properties of the materials being used. By mastering these aspects, you can unlock a world of creative possibilities and produce coasters that are truly unique and exceptional. So, let's dive into the 5 laser cut coaster tips that will help you achieve perfection.
Understanding Laser Cutting Technology

Tip 1: Choose the Right Material
The material you choose for your laser cut coasters can make all the difference in terms of durability, appearance, and functionality. Popular materials for laser cut coasters include wood, bamboo, and acrylic. Each material has its unique characteristics, and some are better suited for certain designs and applications. For example, wood is a great choice for a rustic or traditional look, while acrylic is ideal for a modern and sleek design.Designing for Laser Cutting

Tip 2: Optimize Your Design for the Material
To ensure that your design is optimized for the material, you need to consider the cutting speed, power, and frequency of the laser. Different materials require different settings, and using the wrong settings can result in a poor-quality cut or even damage to the material. For example, cutting through thick wood requires a slower speed and higher power, while cutting through thin acrylic requires a faster speed and lower power.Working with Different Materials

Tip 3: Consider the Thickness and Density of the Material
The thickness and density of the material can significantly impact the cutting process. Thicker materials require more power and a slower cutting speed, while thinner materials require less power and a faster cutting speed. Understanding the thickness and density of the material will help you optimize your design and achieve a smooth, even cut.Adding a Finish to Your Coasters

Tip 4: Apply a Finish to Protect the Material
Applying a finish to your coasters can help protect the material from spills and stains, making them easier to clean and maintain. A finish can also enhance the appearance of the coasters, adding a touch of elegance and sophistication to your decor. When choosing a finish, consider the material and the desired look, and make sure to follow the manufacturer's instructions for application and drying times.Assembling and Packaging Your Coasters

Tip 5: Add a Personal Touch to Your Coasters
To make your coasters truly unique and special, consider adding a personal touch. This can include engraving a message or design onto the coaster, adding a custom shape or size, or using a unique material or finish. A personal touch can make your coasters stand out and add a touch of personality to your decor.Laser Cut Coaster Image Gallery










What is the best material for laser cut coasters?
+The best material for laser cut coasters depends on the desired look and functionality. Popular materials include wood, bamboo, and acrylic.
How do I optimize my design for laser cutting?
+To optimize your design for laser cutting, consider the material being used, the cutting speed, power, and frequency of the laser, and the desired level of detail and complexity.
Can I add a finish to my laser cut coasters?
+
How do I assemble and package my laser cut coasters?
+To assemble and package your laser cut coasters, consider adding a backing material, such as cork or felt, to the bottom of the coasters, and packaging them in a decorative box or bag.
Can I customize my laser cut coasters with a personal message or design?
+
In
Final Thoughts
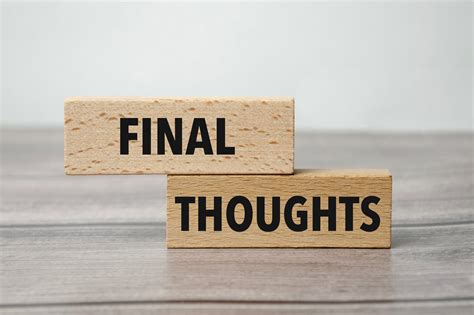