Intro
Discover FRC 3D printable wiring solutions, featuring customizable robotic wire management systems, modular cable organizers, and innovative 3D printed electrical components for efficient robot builds.
The world of robotics and electronics has witnessed significant advancements in recent years, with the rise of 3D printing technology being a key factor in this growth. One area that has particularly benefited from this development is the creation of custom wiring solutions for robotics and electronics projects. For robotics enthusiasts and engineers working with the FIRST Robotics Competition (FRC) platform, 3D printable wiring solutions have become an essential tool in their toolkit. In this article, we will delve into the importance of 3D printable wiring solutions for FRC teams and explore the various benefits and applications of this technology.
The complexity of robotics and electronics projects often requires customized wiring solutions to ensure efficient and reliable performance. Traditional wiring methods can be time-consuming, prone to errors, and may not provide the desired level of flexibility. This is where 3D printing comes into play, offering a rapid and cost-effective way to create custom wiring solutions tailored to specific project requirements. By leveraging 3D printing technology, FRC teams can now design and manufacture complex wiring harnesses, cable management systems, and other electrical components with ease.
Introduction to 3D Printable Wiring Solutions

Benefits of 3D Printable Wiring Solutions
The benefits of 3D printable wiring solutions for FRC teams are numerous. Some of the key advantages include: * Rapid prototyping and production: 3D printing enables the rapid creation of custom wiring solutions, allowing teams to test and iterate on their designs quickly. * Customization: 3D printing allows for the creation of customized wiring solutions tailored to specific project requirements, reducing the need for costly and time-consuming modifications. * Improved reliability: 3D printed wiring solutions can be designed to minimize the risk of electrical failures, ensuring reliable performance in demanding environments. * Reduced weight and size: 3D printed wiring solutions can be designed to be compact and lightweight, making them ideal for robotics and electronics applications where space and weight are limited.Designing 3D Printable Wiring Solutions
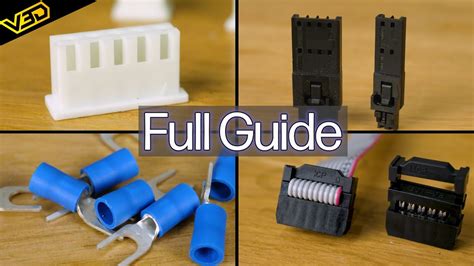
Materials and Technologies Used
A range of materials and technologies can be used to create 3D printable wiring solutions, including: * Conductive filaments: Specialized 3D printing filaments that can conduct electricity, allowing for the creation of custom wiring and electrical components. * Insulating materials: Materials used to insulate wires and electrical components, preventing electrical shorts and ensuring reliable performance. * 3D printing technologies: Fused deposition modeling (FDM), stereolithography (SLA), and selective laser sintering (SLS) are common 3D printing technologies used to create custom wiring solutions.Applications of 3D Printable Wiring Solutions

Case Studies and Examples
Several case studies and examples demonstrate the effectiveness of 3D printable wiring solutions in real-world applications. For instance: * A team of robotics engineers used 3D printing to create a custom wiring harness for a robotic arm, reducing production time and improving reliability. * An electronics manufacturer used 3D printing to create custom PCBs and wiring solutions for a new product line, reducing production costs and improving performance.Challenges and Limitations
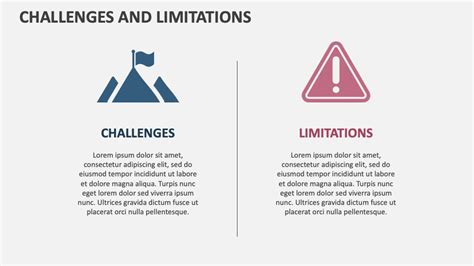
Future Developments and Trends
The field of 3D printable wiring solutions is rapidly evolving, with several future developments and trends on the horizon. Some of the key areas of research and development include: * Advanced materials: The development of new 3D printing materials with improved electrical properties and reliability. * Improved printing technologies: The development of faster and more accurate 3D printing technologies, enabling the production of complex wiring solutions. * Integration with other technologies: The integration of 3D printing with other technologies, such as artificial intelligence and robotics, to create more advanced wiring solutions.FRC 3D Printable Wiring Solutions Image Gallery
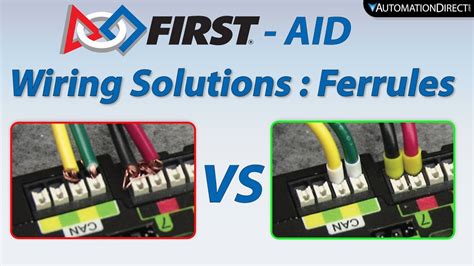
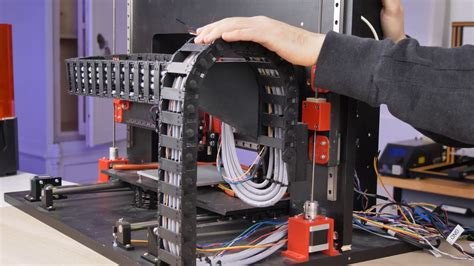
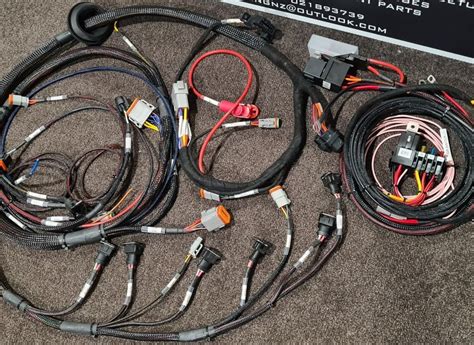
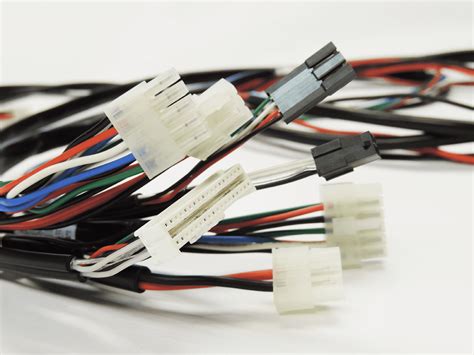
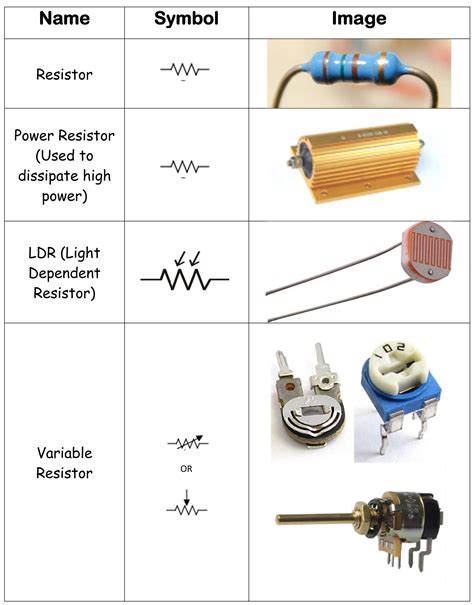
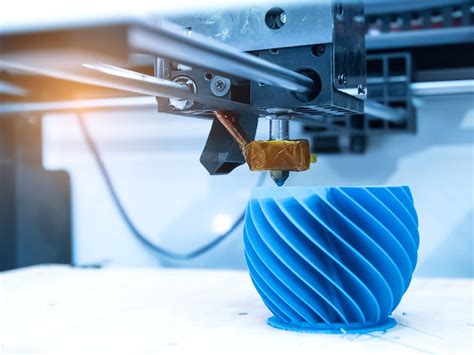
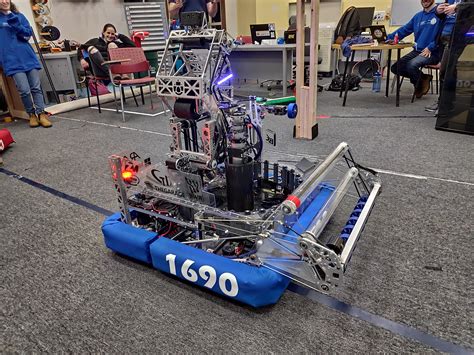
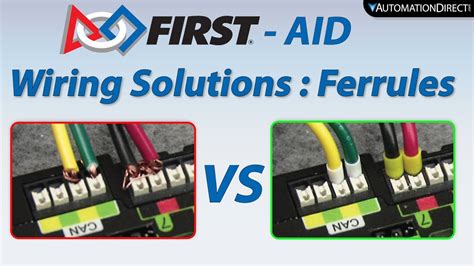
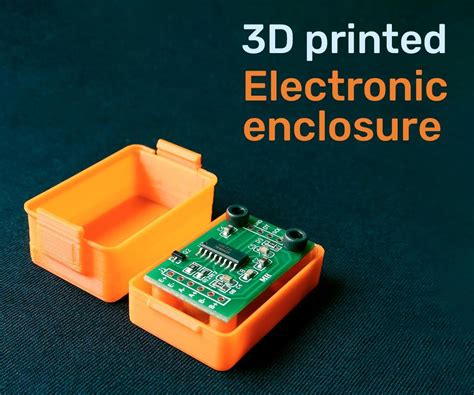
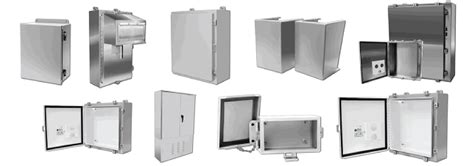
What are the benefits of using 3D printable wiring solutions for FRC teams?
+The benefits of using 3D printable wiring solutions for FRC teams include rapid prototyping and production, customization, improved reliability, and reduced weight and size.
What materials and technologies are used to create 3D printable wiring solutions?
+A range of materials and technologies can be used to create 3D printable wiring solutions, including conductive filaments, insulating materials, and 3D printing technologies such as FDM, SLA, and SLS.
What are some of the challenges and limitations of using 3D printable wiring solutions?
+Some of the challenges and limitations of using 3D printable wiring solutions include material properties, scalability, and cost.
In conclusion, 3D printable wiring solutions offer a range of benefits for FRC teams, including rapid prototyping and production, customization, improved reliability, and reduced weight and size. By leveraging 3D printing technology, teams can create custom wiring solutions tailored to their specific needs, reducing the risk of errors and improving overall system performance. As the field of 3D printable wiring solutions continues to evolve, we can expect to see new developments and trends emerge, further expanding the possibilities for FRC teams and other applications. We invite you to share your thoughts and experiences with 3D printable wiring solutions in the comments below, and to explore the many resources and tutorials available online to learn more about this exciting technology.